Rotor Test Stand
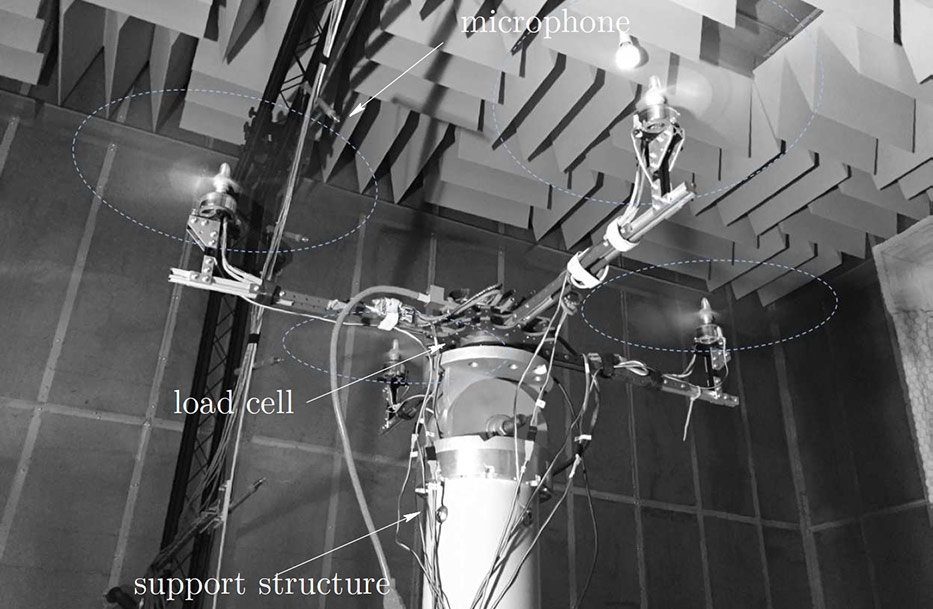
Rotor Test Stand
The rotor test stand at ARL:UT was erected in 2010 for the purposes of conducting wind tunnel studies of rotors in hover and forward flight. The base of the structure and motor housing remains unchanged. The latter of these encompasses a 9 kW electric motor powered by a 10 kW (max) Lambda TKE ESS 50-200 programmable direct current (DC) power supply that outputs up to 50 V and 200 A uninterrupted. The maximum rotational speed of the motor is 8,000 RPM (133 rot/s) with a maximum torque of 10Nm. The motor is encased in an aluminum shell in order to reduce motor noise from contaminating acoustic measurements. Installed on the motor casing is a 1∕rev magnetic pickup that captures motor rotation speed. The entire assembly is mounted to a heavy metal pipe that elevates the rotor disk plane 105 in. above the laboratory floor in order to minimize ground effects. An illustration of the rotor test stand is shown in Figure 1a. Over the years the upper assembly has been modified to accommodate a variety of rotor configurations as shown in Figures 2 through 4. These comprise single blade rotors (Mula & Tinney 2015), two and four bladed rotors (Mula, et al. 2013), stacked counter-rotating rotors (Mula, et al. 2014), stacked co-rotating rotors (Tinney & Valdez 2020), as well as quadcopter, hexacopter and octocopter configurations as they relate to small UAV / drone type platforms (Tinney & Sirohi 2018).
- Mula, Tinney (2015),
A study of the turbulence within a spiraling vortex filament using proper orthogonal decomposition,
J. Fluid Mech., v. 769, pp. 570-589, DOI: 10.1017/jfm.2015.104. - Mula, Stephenson, Tinney, Sirohi, (2013),
Dynamical characteristics of the tip vortex from a four-bladed rotor in hover,
Exp. Fluids, v. 54, no. 1600, DOI: 10.1007/s00348-013-1600-9. - Tinney, Sirohi, (2018),
Multirotor drone noise at static thrust,
AIAA Journal, v. 56, no. 7, 2816–2826, DOI: 10.2514/1.J056827. - Tinney, Valdez (2020),
Thrust and acoustic performance of small-scale, coaxial, co- rotating rotors in hover,
AIAA Journal, v. 58, no. 4, 1657–1667, DOI: 10.2514/1.J058489. - Mula, Cameron, Tinney, Sirohi, (2014),
Low-dimensional characteristics of tip vortices from a coaxial rotor in hover,
American Helicopter Society 70th Annual Forum, Montreal, Canada, May.
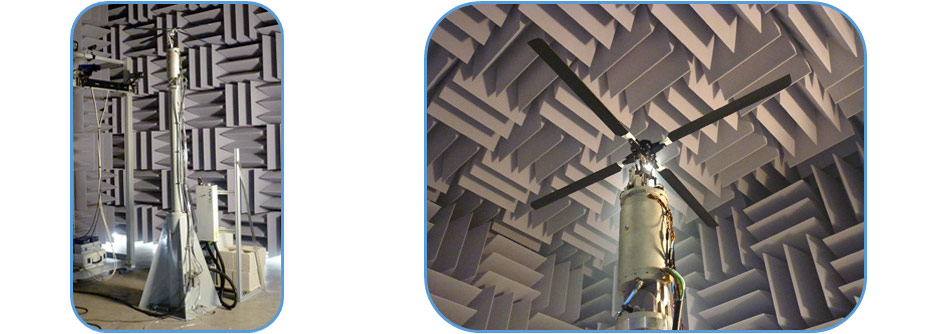
Figure 1: (a) Rotor Test Stand installed in PRC Building 124. (b) Upper assembly with four bladed rotor.
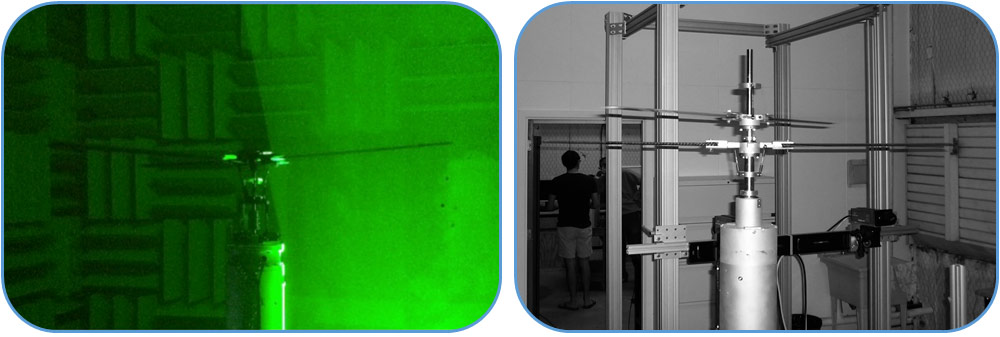
Figure 2: (a) PIV measurements with the four bladed rotor. (b) Upper assembly with stacked, counter-rotating rotor.
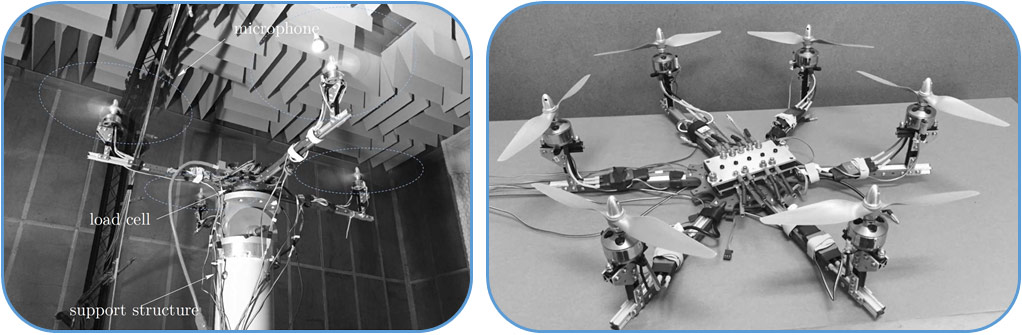
Figure 3: (a) Acoustic measurements of a quadcopter. (b) Hexacopter configuration.
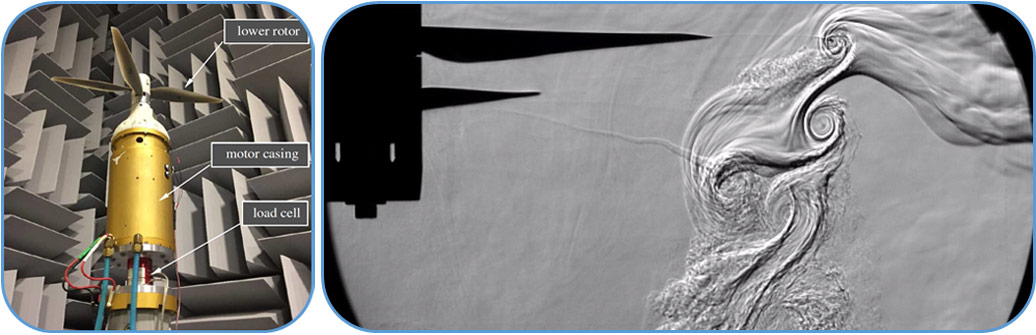
Figure 4: (a) Stacked co-rotating rotor. (b) High-speed schlieren images of the stacked co-rotating rotor in hover.